The Mini-Excavator
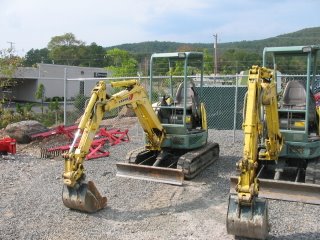
So, now that the basement slab is poured, we can get started on the last of the footers. I call up the backhoe operator who dug all the other footers and he says he can’t get to me for a month; and worse yet, he doesn’t know anyone who has a backhoe as small as his; ie one that can get into and work effectively on my narrow, tight lot. Renting something appears to be the only alternative; and he suggests trying out a “trac-hoe”. I call around town and check out backhoes and trac-hoes; they rent for about the same thing; so I go with the trac-hoe.
I have never had more fun playing in the dirt. The rental place gives you a mini-tutorial on what the controls do, but it took at least an hour of hands-on to get the basics down. Several times I’d get a bucket full of dirt picked up, and be ready to swing the boom left to dump it on my pile. Well, left hand swings the boom, but right hand dumps the bucket. You guessed it, I moved the right hand, and immediately dumped the dirt back into ditch. So, you laugh a little at your own clumsiness and then go do it again.
After the second hour you’d think I’d been operating this thing for years. I was able to use both hands at the same time; ie raise AND swing the boom at the same time, then dump the bucket while the boom was still extending.
It only took three hours to dig all my remaining footers. I’d paid for a whole day of use (8 hours of digging on the hour-meter), so I begin to think of what other trouble I could get myself into with this thing. My building site is not as smooth as I’d like; a few dips and high spots; but not anymore. The trac-hoe has a bulldozer blade which moves earth very effectively, but that earth is on the “other” side of the ditch I just dug. So, now the fun part is how to cross the ditch. I had seen my backhoe operator put the “front” bucket down on the ground and use it to lift up the front end of his tractor so his smaller front tires wouldn’t get caught in the ditch. He would then power forward with his rear tires and use the front bucket as a skid to slide on; making it into kind of a tricycle. So, I tried this with the trac-hoe and it works beautifully. I had previously discussed this with the rental place manager to make sure it was okay. You, the renter are responsible for any damage of an “unusual” nature; such as letting the trac-hoe fall over on it’s side. This thing weighs 5,000 pounds and I could have nightmares trying to figure out how to get it back upright if it fell over on my lot. There is NO room to get a real wrecker in there if you need one, so CAUTION is the name of the game today (actually, it’s the name of the game every day).
After all the lot smoothing was done I still had hours left, so I dug a small drainage ditch in front and used the dirt to fill in two holes. All together; time used; four hours; and three gallons of diesel (you have to return the unit with a full tank). I could have rented it for a half day (and saved $30).