Rebar Safety
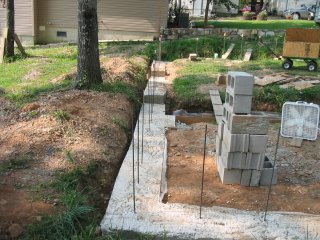
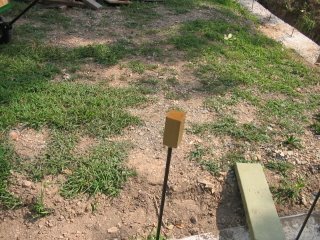
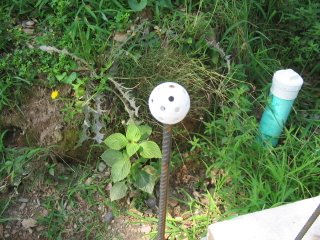
Imagine for a moment, that you are working on your dream house -- alone -- everybody else is at work, and none of the neighbors are at home. You're carrying something, you trip on a loose rock, fall, and skewer yourself on one of these many vertical rebars. Not a pretty picture; worse, even if you have that cell phone in your pocket and are conscious enough to call 911 you still might die before the ambulance arrives.
I found out the hard way that these cut rebar ends are very sharp; like razor sharp. They will slice you open just like a scalpel (another excellent reason for keeping the tetanus shot up to date). No, I didn't skewer myself, but I have brushed up against them a time or two and been scratched pretty good.
So, I decided to do something about it. First, I tried putting the plastic golf balls on top of each piece (pic #3). That works well to prevent scratches, but it wouldn't prevent the skewering fall. So, then came the 2x2 wooden blocks, drilled halfway thru lengthwise with a 1/2" spade bit. Now, these things work. I've put my weight down on them and they hold me up. If you fall on one, it will hurt like the dickens, but it might prevent an untimely trip to the morgue.
Build safe guys.